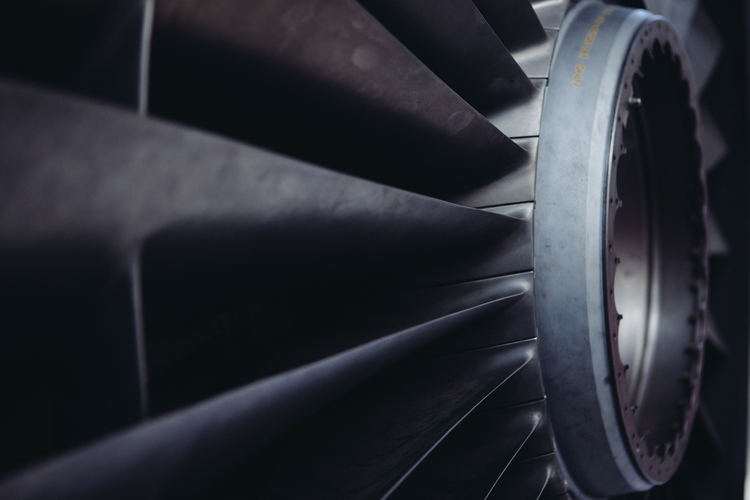
Fast Fan
A rim-driven future? Wrexham University’s FAST-Fan project
Wrexham University are leading a consortium of industrial drone and electrical propulsion companies in the development of a novel type of ducted fan for high-speed electrically powered flight. Electrical propulsion heralds an exciting era in aeronautical engineering, with the goal being zero emission flight accompanied by zero reduction in operational capabilities. The importance of protecting the environment and energy supply by reducing aircraft emissions is a key priority in the European Commission’s report “Flightpath 2050 Europe’s Vision for Aviation” and although this may appear a distant aspiration, the tasks associated with overcoming the technical problems are already well underway.
One of the major challenges to be met is how to achieve efficient high-speed flight using electrical motor technology. The WEFO funded “Fast-Fan” project involves Wrexham University collaborating with their industrial partners to develop an innovative high-thrust electric fan configuration. The novel fan technology will offer the potential advantages of reduced obstruction to air-flow and multi-stage compression. The Fast-Fan design will also minimise losses and improve the aircraft’s handling and performance. Glyndwr University are developing a prototype “technology demonstrator” for flight testing in an unmanned aircraft and believe this technology to be the ideal solution for distributed-thrust and future high-speed aircraft propulsion applications.
The Fast-fan is being developed to satisfy the demands of an aerospace sector that is expected to be the fastest growing in the coming years with the development of new urban mobility applications such as flying taxis, delivery drones and autonomous vehicles.
The technical and research challenges are significant, involving:
- The design and integration of the electromagnetic components of the ducted fan and in the control of its rotor assembly
- The mechanical challenges associated with this novel motorised fan configuration
- A lightweight structural design required for the body structure and inlet and exhaust duct manufacture
- Overcoming the issues relating to high torque, heat and vibration
- Ensuring that the electrical control of the motor and commutation of the windings underpins motor performance
The industrial partners each bring valuable specialist skills and experience to the project. The partners are Motor Design Ltd, Invertek UK Ltd, Geola Technologies Ltd, Ad-Manum UAS Technologies Ltd.