Research Seminar Series #5 - Technology and Engineering
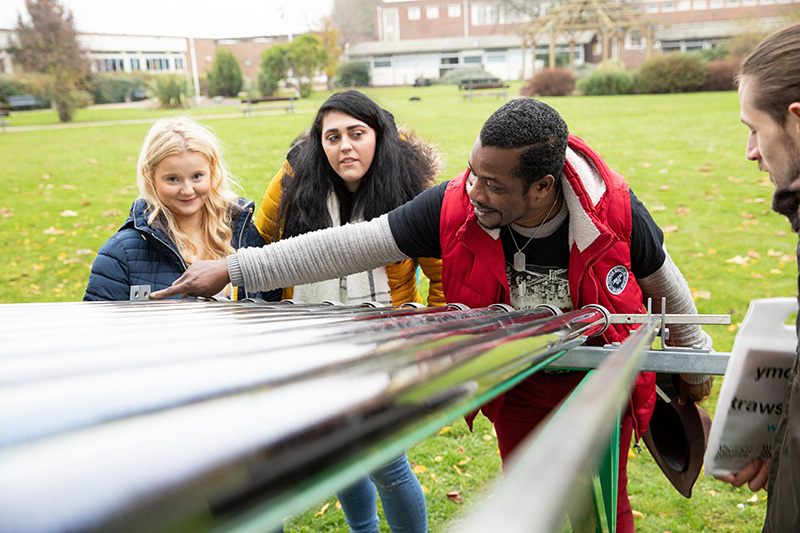
January 2024
January saw the FAST Research Series recommence for the new year, with Dr Rob Bolam chairing the Technology and Engineering seminar.
Nikolas Veillet and Marin Gaillard joined the seminar to talk about the Quick Electric System Technology (QuEST) project in Uncrewed Aerial Vehicles (UAV), that is underway in the Engineering department.
Nikolas and Marin are MSc Aeronautical Engineering students who, alongside eight other students from across Europe, are researching, designing and building a large UAV. The vehicle will use a new electrical propulsion system, working alongside the FAST Fan project. The FAST fan is the world’s first rim-driven fan created by Dr Rob Bolam and Research Assistant / PhD Student Jhon Paul Roque, in collaboration with industry. The FAST Fan aims to support the journey to net zero; you can find out more by watching Dr Rob Bolam’s Public Lecture and reading Jhon Paul Roque’s Research Seminar Blog.
The QuEST team have split the project into various workflow tasks: Flight Control System, Fuselage, Wings, Tailplane, Landing Gear/ Brakes and Management & Regulation Conformity.
Nikolas gave the audience insight into the research and design of the landing gear, with the team having opted for a tricycle undercarriage for a number of reasons, including the singular centre of gravity due to the electrical propulsion design.
The team are also undertaking research into the best shapes and materials for the main gear frame and nose gear. Using structural analysis software, the placement of materials is being considered at a layering level, rather than viewing it as just a block structure. As a result, the team have altered the manufacturing process, using a wraparound process which yields much more efficient results than using traditional moulds.
Marin talked us through the flight control system design which will use a high-power motor driving system. The conformity requirements were also discussed, as the UAV is expected to weigh around 40kg and conformity requirements apply to 25kg+ UAVs. One of the requirements is autonomous flight mode for safe return, requiring the ability to programme a GPS route for return in the event of control failure. The QuEST control design is complex, with a number of challenges such as high-power issues and diverse electrical rating across the various components/devices. Research is also being conducted to try to improve the semiconductors used in electrical propulsion, enabling new design paradigms and different topology.
All in all, this is a very exciting project that is advancing the design, and hopefully in turn the performance of UAV’s and we look forward to seeing the outcomes as the project progresses. Thank you to Nikolas and Marin for sharing the detail and presenting to an audience of academics, which is never easy, but you were undeterred. Thank you!
Andrew Sharp, Senior Lecturer in Electrical Engineering, then delivered a session on Temperature Gradient Improvement of Power Semiconductor Modules Mounted on a Forced Air Heat Sink.
Andrew began by detailing the motivation behind the research, which is his current PhD project. A high percentage of component failures in power electronic devices are due to the failure of convertor power semiconductors. Heat losses in power semiconductors are generally managed using a heat sink, which transfers the heat from the semiconductor component to the environment usually by using forced air cooling. Imagine, a block of aluminium with fins cut into the bottom, to transfer heat away from the semiconductor device using a fan located at one end. However, this causes a temperature difference (gradient) along the length of the heat sink which, you guessed it, creates mechanical stress in the structure of the semiconductor due to different materials having different rates of thermal expansion. Mechanical stresses mean reduced reliability and lifespan of the modules.
So, Andrew is trying to find a solution to this issue by modifying a standard heat sink to implement variable thermal resistances along the heat sink length. Below is an image of a standard heat sink alongside novel heatsink designs that Andrew came up with as possible replacements for the standard ‘fin’ design.
Andrew established that it is more efficient to raise all components to the same temperature by mechanically modifying the heat sink in order to degrade the heat transfer conditions. Computer simulation supported the theory that heat sink alterations (such a v-cut) alters airflow across the heat sink and improves the temperature gradient on the surface area of the heatsink. However, computer simulation alone is not enough, and it was determined that physical measurements would be required to validate the results.
In 2023, Andrew set about obtaining grant funding to build a bespoke test rig to make the required physical measurements; he was successful, and the test rig has now been built. The temperature readings obtained using this test rig will be compared to those obtained by computer simulation and hopefully provide validation of the computer simulation results.
Further work is required to measure the temperature and volume of air flow through the heatsink and this data will need to be added to the computer model. Andrew’s end goal is to obtain comparable readings between the computer simulation and practical approaches, and in that respect, the project is still ongoing. A number of papers have however been published along the way and we look forward to the next phase of the project.
Andrew’s passion and enthusiasm was evident throughout the session, making it all the more engaging and accessible, even for those audience members (like us) who were unfamiliar with heat sinks! Thank you Andrew.
Published works:
A.Mueller, C. Buennagel, S. Monir, A. Sharp, Y. Vagapov and A. Anuchin, “Numerical Design and Optimisation of a Novel Heatsink using ANSYS Steady-State Thermal Analysis,” in Proc. 27th Int. Workshop on Electric Drives (IWED), Moscow, Russia, 2020, pp. 1-5,
C. Bünnagel, S. Monir, A. Sharp, A. Anuchin, O. Durieux, I. Uria, and Y. Vagapov, “Forced air cooled heat sink with uniformly distributed temperature of power electronic modules,” Applied Thermal Engineering, vol. 199, Nov. 2021, Art no. 117560
A.Sharp, S. Monir, Y. Vagapov and R. J. Day, "Temperature Gradient Improvement of Power Semiconductor Modules Cooled Using Forced Air Heat Sink," 2022 XIV International Symposium on Industrial Electronics and Applications (INDEL), 2022, pp. 1-5
A. Sharp, S. Monir, R. J. Day, Y. Vagapov and A. Dianov, “A test rig for thermal analysis of heat sinks for power electronic applications,” in Proc. 19th IEEE East-West Design & Test Symposium (EWDTS), Batumi, Georgia, 22-25 Sept. 2023, pp. 1-4,